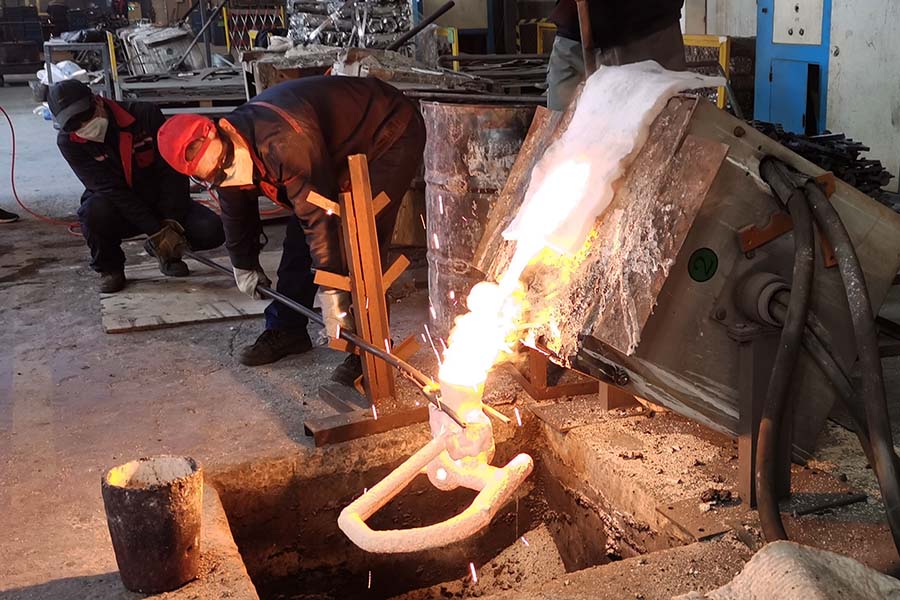
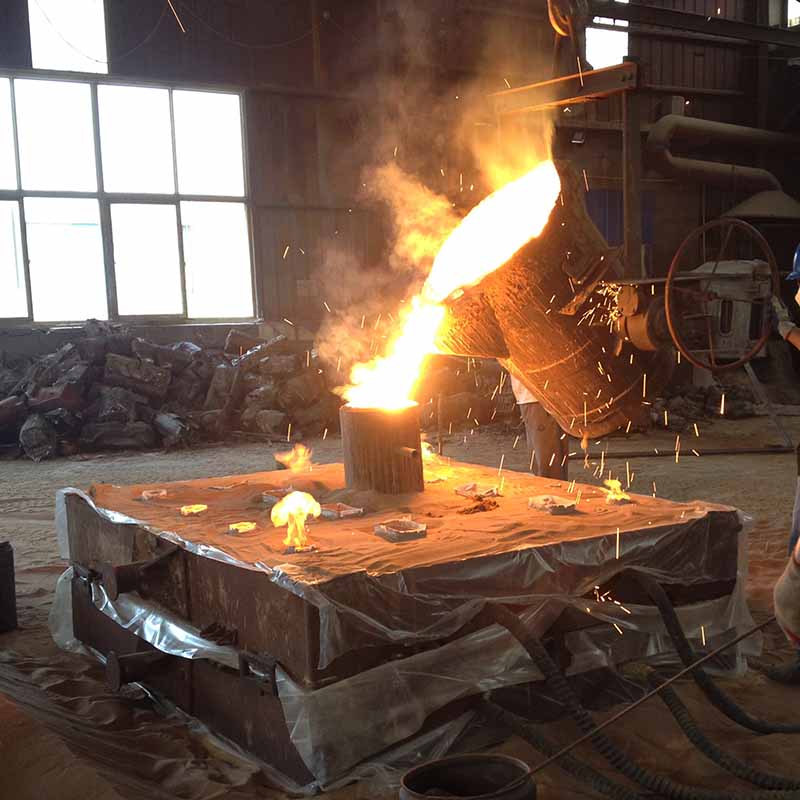
Turnarea este una dintre cele mai vechi metode de modelare a metalelor cunoscute de ființe umane. În general, înseamnă turnarea metalului topit într-o matriță refractară cu o cavitate de forma care urmează să fie realizată și lăsarea acestuia să se solidifice. Cândsolidificat, obiectul metalic dorit este scos din matrita refractara fie prin spargerea matritei, fie prin desfacerea matritei. Obiectul solidificat se numește turnare. Acest proces se mai numește și fondare, iar fabrica modernă care se concentrează pe turnarea pieselor metalice se numeșteturnătorie.
1. Istoria procesului de turnare
Procesul de turnare a fost probabil descoperit în jurul anului 3500 î.Hr. în Mesopotamia. În multe părți ale lumii în acea perioadă, topoarele de cupru și alte obiecte plate erau turnate în forme deschise din piatră sau coapte.lut. Aceste matrițe erau în esență dintr-o singură bucată. Dar în perioadele ulterioare, când erau necesare obiecte rotunde, astfel de matrițe au fost împărțite în două sau mai multe părți pentru a facilita retragerea obiectelor rotunde.Epoca bronzului (c 2000 î.Hr.) a adus mult mai mult rafinament în procesul de turnare. Poate pentru prima dată, a fost inventat un miez pentru a face buzunare goale în obiecte. Aceste miezuri au fost făcute din lut copt.De asemenea, procesul de cire perdue sau ceară pierdută a fost utilizat pe scară largă pentru realizarea de ornamente și lucrări fine.
Tehnologia de turnare a fost mult îmbunătățită de chinezi din jurul anului 1500 î.Hr. Înainte de aceasta, nu există dovezi ale vreunei activități de turnare găsite în China. Nu par să fi fost grozaviFamiliar cu procesul cire perdue și nici nu l-a folosit pe scară largă, ci s-a specializat în matrițe din mai multe piese pentru realizarea unor lucrări extrem de complicate. Au petrecut mult timp perfecționând matrița până la ultimul detaliu, așa că cu greuorice lucrare de finisare a fost necesară la turnarea realizată din matrițe. Probabil că au făcut matrițe cu piese care conțineau piese montate cu grijă, în număr de treizeci sau mai mult. De fapt, multe astfel de matrițe au fost dezgropateurmând săpături arheologice în diferite părți ale Chinei.
Civilizația din Valea Indusului este cunoscută și pentru utilizarea pe scară largă a turnării de cupru și bronz pentru ornamente, arme, unelte și ustensile. Dar nu au fost multe îmbunătățiri în tehnologie. Din variaObiecte și figurine care au fost excavate din siturile din Valea Indusului, par să fi fost familiarizați cu toate metodele de turnare cunoscute, cum ar fi matrița deschisă, matrița pe bucată și procesul de cire perdue.
Deși India ar putea fi creditată cu invenția oțelului creuzet, nu prea mult din temelia de fier a fost evidentă în India. Există dovezi că întemeierea fierului a început în jurul anului 1000 î.Hr. în Siria și Persia. Aparecăturnare de fiertehnologia din India a fost folosită încă de pe vremea invaziei lui Alexandru cel Mare, în jurul anului 300 î.Hr.
Faimosul stâlp de fier aflat în prezent lângă minarul Qutb din Delhi este un exemplu al abilităților metalurgice ale indienilor antici. Are 7,2 m lungime și este fabricat din fier maleabil pur. Acesta se presupune a fi dinperioada Chandragupta II (375-413 d.Hr.) a dinastiei Gupta. Rata de ruginire a acestui stâlp, care stă afară în aer liber este practic zero și chiar și porțiunea îngropată ruginește într-un ritm extrem de lent. Acesttrebuie să fi fost mai întâi turnat și apoi ciocănit până la forma finală.
2. Avantaje și limitări
Procesul de turnare este utilizat pe scară largă în producție datorită numeroaselor sale avantaje. Materialul topit curge în orice secțiune mică din cavitatea matriței și, ca atare, în orice formă complicată - internăsau extern – poate fi realizat cu procesul de turnare. Este posibil să turnați practic orice material, fie el feros sau neferos. În plus, instrumentele necesare pentru turnarea matrițelor sunt foarte simple șiieftin. Ca urmare, pentru producția de probă sau pentru producția unui lot mic, este o metodă ideală. Este posibil în procesul de turnare, să plasați cantitatea de material acolo unde este exact necesar. Ca urmarese poate realiza reducerea greutății în proiectare.Turnărisunt în general răcite uniform din toate părțile și, prin urmare, se așteaptă să nu aibă proprietăți direcționale. Există anumite metale și aliajecare poate fi prelucrat numai prin turnare și nu prin orice alt procedeu precum forjare din cauza considerentelor metalurgice. Se pot face turnări de orice dimensiune și greutate, chiar și până la 200 de tone.
Cu toate acestea, precizia dimensională și finisarea suprafeței obținute prin normalprocesul de turnare cu nisipnu ar fi adecvată pentru aplicarea finală în multe cazuri. Pentru a lua în considerare aceste cazuri, niște turnare specialeau fost dezvoltate procese precum turnarea sub presiune, ale căror detalii sunt date în capitolele ulterioare. De asemenea, procesul de turnare cu nisip necesită într-o oarecare măsură forță de muncă și, prin urmare, sunt vizate multe îmbunătățiri,precum turnarea mașinilor și mecanizarea turnătorii. Cu unele materiale, este adesea dificil de îndepărtat defectele care decurg din umiditatea prezentă înturnări de nisip.
3. Condiții de casting
În capitolele următoare vor fi văzute detaliile turnării în nisip, care reprezintă procesul de bază al turnării. Înainte de a intra în detaliile procesului, ar fi să definiți un număr de cuvinte din vocabularul de turnareadecvat.
Balon– Un balon de turnare este unul care ține intactă matrița de nisip. În funcție de poziția balonului în structura matriței, acesta este denumit sub diferite nume, cum ar fi drag, cope și obraz. Este alcătuit din lemnpentru aplicații temporare sau mai general de metal pentru utilizare pe termen lung.
Trageți– Balon de turnare inferior
Faceți față– Balon de turnare superior
Obraz– Balon de turnare intermediar folosit la turnarea din trei piese.
Model– Modelul este o replică a obiectului final care urmează să fie realizat cu unele modificări. Cavitatea matriței este realizată cu ajutorul modelului.
Linie de despărțire– Aceasta este linia de despărțire dintre cele două baloane de turnare care formează matrița de nisip. În modelul split este, de asemenea, linia de despărțire dintre cele două jumătăți ale modelului
Placa de jos– Aceasta este o placă realizată în mod normal din lemn, care este utilizată la începutul fabricării matriței. Modelul se ține mai întâi pe placa de jos, se stropește nisip pe ea și apoi se face baterea în drag.
Cu fața cu nisip– Cantitatea mică de material carbonic presărat pe suprafața interioară a cavității de turnare pentru a oferi un finisaj mai bun al suprafeței pieselor turnate
Nisip de turnare– Este materialul refractar proaspăt preparat folosit pentru realizarea cavității matriței. Este un amestec de argilă de siliciu și umiditate în proporții adecvate pentru a obține rezultatele dorite și înconjoarămodel în timp ce faceți matrița.
Nisip de sprijin– Este ceea ce constituie cea mai mare parte a materialului refractar găsit în matriță. Acesta este alcătuit din nisip uzat și ars.
Miez– Se folosește pentru realizarea de cavități goale în piese turnate.
Bazin de turnare– O mică cavitate în formă de pâlnie în partea de sus a matriței în care este turnat metalul topit.
Spure– Pasajul prin care metalul topit din bazinul de turnare ajunge în cavitatea matriței. În multe cazuri, controlează fluxul de metal în matriță.
Alergător– Căile de trecere din planul de separare prin care fluxul de metal topit este reglat înainte de a ajunge în cavitatea matriței.
Poartă– Punctul efectiv de intrare prin care metalul topit intră în cavitatea matriței.
Coronă– Chaplets sunt folosite pentru a susține miezurile din interiorul cavității matriței pentru a avea grijă de propria greutate și a depăși forțele metalostatice.
Chill– Frigurile sunt obiecte metalice, care sunt plasate în matriță pentru a crește viteza de răcire a pieselor turnate pentru a oferi o viteză de răcire uniformă sau dorită.
Riser– Este un rezervor de metal topit prevăzut în turnare, astfel încât metalul fierbinte să poată curge înapoi în cavitatea matriței atunci când are loc o reducere a volumului de metal din cauza solidificării
4. Procedura de fabricare a mucegaiului cu nisip
Procedura de realizare a unei matrițe tipice de nisip este descrisă în următorii pași:
Mai întâi, o placă de jos este plasată fie pe platforma de turnare, fie pe podea, făcând suprafața uniformă. Balonul de turnare prin tragere este ținut cu capul în jos pe placa de jos, împreună cu partea de tragere amodel în centrul balonului pe tablă. Ar trebui să existe suficient spațiu între model și pereții balonului, care ar trebui să fie de ordinul 50 până la 100 mm. Nisipul uscat este presărat pestetabla și modelul pentru a oferi un strat nelipicios. Nisip de turnare proaspăt pregătit de calitate necesară este acum turnat în drag și pe model la o grosime de 30 până la 50 mm. Restul balonului esteumplut complet cu nisip de rezervă și batut uniform pentru a compacta nisipul. Baterea nisipului trebuie făcută corect pentru a nu-l compacta prea tare, ceea ce face dificilă evacuarea gazelor,nici prea lejer, pentru ca matrita să nu aibă suficientă rezistență. După terminarea batonării, excesul de nisip din balon este complet răzuit folosind o bară plată până la nivelul marginilor balonului.
Acum, cu un fir de aerisire, care este un fir cu un diametru de 1 până la 2 mm, cu un capăt ascuțit, se fac găuri de aerisire în tragere până la adâncimea completă a balonului, precum și la model pentru a facilita îndepărtarea gazelor. în timpul turnăriisolidificare. Acest lucru completează pregătirea dragului.
Balonul terminat este acum răsturnat pe placa de jos, expunând modelul așa cum se arată în fotografie. Folosind un slick, marginile de nisip din jurul modelului sunt reparate și jumătatea de copt a modelului este plasată pestemodelul de tragere, aliniindu-l cu ajutorul diblurilor. Balonul de cope de deasupra tragerii este amplasat aliniind din nou cu ajutorul știfturilor. Nisipul uscat de despărțire este presărat pe toată tragerea și pe model.
Un știft de canalizare pentru realizarea pasajului de canalizare este situat la o distanță mică de aproximativ 50 mm de model. De asemenea, știftul de ridicare, dacă este necesar, este păstrat într-un loc adecvat și nisip de turnare proaspăt preparat similar cu acestade tragere împreună cu nisipul de suport este presărat. Nisipul este bine bătut, excesul de nisip răzuit și găuri de aerisire sunt făcute peste tot în copă, ca și în drag.
Știftul de canalizare și știftul de ridicare e sunt scoase cu grijă din balon. Mai târziu, bazinul de turnare este tăiat aproape de partea superioară a maței. Cope este separat de drag și de orice nisip liber de pe interfața de cope și dragde tragere este suflată cu ajutorul burdufurilor. Acum, jumătățile de cap și modelul de tragere sunt retrase prin utilizarea vârfurilor de tragere și lovirea modelului de jur împrejur pentru a mări ușor cavitatea matriței, astfel încâtpereții mucegaiului nu sunt stricați de modelul de retragere. Galeriile și porțile sunt tăiate în matriță cu grijă, fără a strica matrița. Orice exces sau nisip liber găsit în ghidajele și cavitatea mucegaiului este suflatdeparte folosind burduful. Acum, nisipul de fațare sub formă de pastă este aplicat pe toată cavitatea matriței și pe canale, ceea ce ar oferi turnării finite un bun finisaj de suprafață.
Un miez de nisip uscat este pregătit folosind o cutie de miez. După coacere adecvată, se pune în cavitatea matriței așa cum se arată în fotografie. Coperta se inlocuieste pe drag avand grija de alinierea celor doua prin intermediulace. O greutate adecvată este păstrată pe copa pentru a avea grijă de forța metalostatică ascendentă în timpul turnării metalului topit. Acum matrița, așa cum se arată în fotografie, este gata pentru turnare.
Ora postării: 25-dec-2020